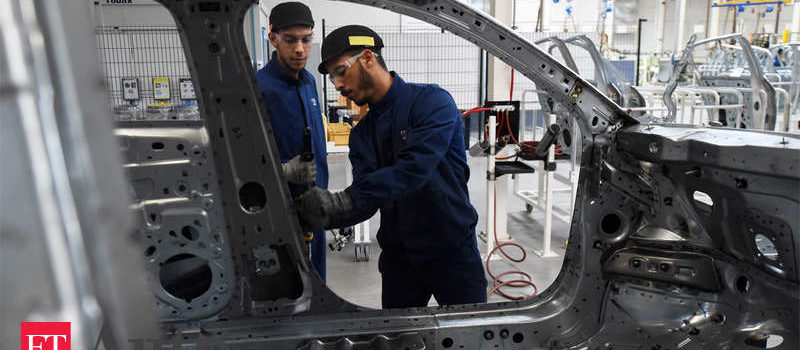
$3 billion cash flows stuck on account of lockdown, auto parts companies urge vehicle makers to release timely payment – ET Auto
More than 100 component makers have already made an advance payment to 100,000 blue-collared workers a fortnight before the scheduled date of payment. Mumbai: 21 days lock down would choke fledgling Indian auto component industry with over a $3 billion or Rs 25000 crore of cash flows.Having [...]